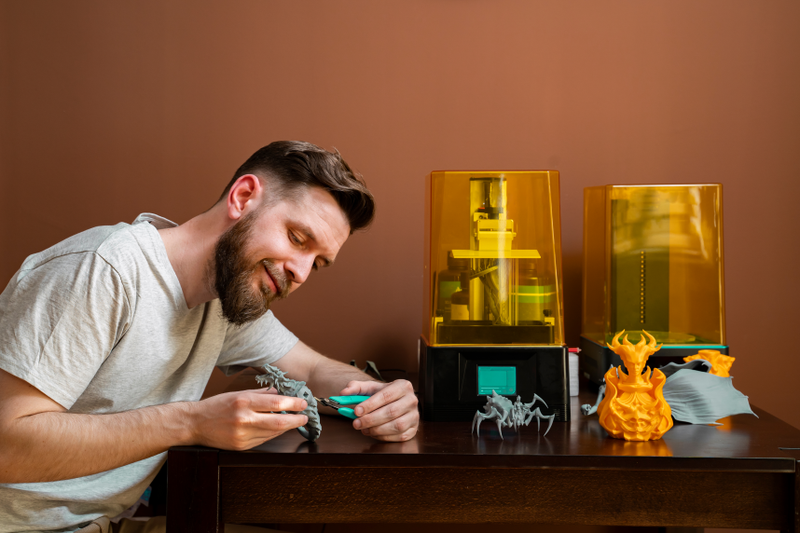
3D printers are changing the face of production as we know it. In this article, we consider what is 3D printing, and how exactly does it work?
What is a 3D Printer?
A 3D printer is a type of printer that’s able to produce a three-dimensional object based on computer-aided designs (CAD). Rather than relying on factory processes or third-party manufacturing, 3D printing allows anybody to create prototypes and objects from their home office or warehouse. 3D printers also allow for more complex designs than many traditional manufacturing processes can achieve, making it easier to create complex, high-quality items in a lot less time.
3D printing has led to notable breakthroughs in fields like healthcare, where 3D printers have been put to use for everything from creating spare ventilator parts to replicating human organs. 3D printers that don’t require any tooling have also opened the doors for simplified, at-home manufacturing for everyone.
How Does a 3D Printer Work & What is the Printing Process?
So, how does 3D printing work?
When it comes down to it, the process of a 3D printer isn’t all that different to what 2D inkjet printers have been doing for years. Yet, while 2D printers use ink to create text or images, 3D printing, which is sometimes also referred to as ‘additive manufacturing’, involves layering materials like plastics or composites to create objects based on CAD designs. In other words, you can sit at home and create a file on your computer, then click ‘print’ and watch your 3D printer get to work.
A 3D printer will create potentially thousands of these super thin layers from the bottom up to create everything from hollow objects to items with internal moving parts. None of which is possible with traditional manufacturing. 3D printers use a variety of technologies to achieve this goal, which commonly include material extrusion, energy deposition, and polymerisation.
3D printing is ideal for both high-end manufacturing projects and at-home printing, and requires only a basic step-by-step process as follows –
- Designing: To begin printing, you’ll need to develop a CAD design, either using 3D printing software or using a free design that you can find online. You’ll then need to export this design as an STL file, which will store information about your 3D object. Once you’ve done that, it’s beneficial to start ‘slicing’ your design in software created for this purpose. This process involves breaking your design down into layers, which allows your printer to understand everything from the amounts of materials required to the exact dimensions of your object.
- Printing: Set up your 3D printer by ensuring things like your chosen materials and 3D printer accessories like the size of the nozzle you’re using. Send your file to your 3D printer by either loading it into a USB or sending it directly via your printer’s interface. The amount of printing time you can expect may vary from a few hours to a couple of days, depending on things like the size and detail of your design.
- Post-processing: Most 3D models will require some finishing steps, including sanding, colouring, and polishing. Models that contain multiple parts which are each printed separately will require welding and assembly to create complete models. 3D printed models also require cleaning after printing to remove things like excess resin or filament from the surface. You should do this using isopropyl alcohol or similar products.
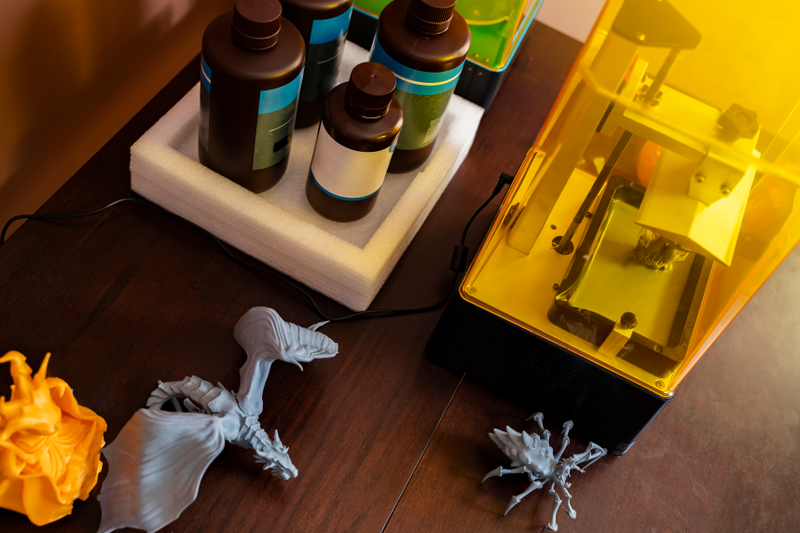
Types of 3D Printer
The term ‘3D printing’ covers several different technologies which create 3D objects in slightly different ways. All of these printers use a layering technique but vary in their use of materials, the finishes they produce, and the objects they’re best suited to.
The three most prominent 3D technologies to consider in your printing journey include –
Selective Laser Sintering (SLS)
SLS 3D printers use a high-power laser to sinter particles of polymer powder into solid structures on a layer-by-layer basis. SLS parts can have a slightly rough finish, but they benefit from almost no visible layer lines and a level of integrity that saves the need for specific support structures. SLS can also produce highly accurate parts.
Nylon is the most common material used in SLS printing, followed by materials like polypropylene, and thermoplastic polyurethane. Each of these materials is used in powder form and can create durable models.
SLS is best used for applications that require robust highly complex parts, such as –
- Durable manufacturing aids and parts
- Medical device functional prototyping
- Custom manufacturing
Stereolithography (SLA)
SLA belongs to a group of 3D printing technologies known as VAT photopolymerization, and was the first ever 3D printing technology, developed way back in the 1980s. This technique remains a favourite for many professionals and involves the use of a laser to cure liquid resin into a hardened plastic. This is the process of ‘photopolymerisation’.
The ongoing popularity of SLA printers is, in large part, thanks to their ability to create highly detailed prototypes. SLA printing also benefits from smooth finishes and typically watertight models. These benefits were once restricted by large-scale hardware, but the development of smaller format desktop SLA printers has brought this process within much easier reach for even at-home printing projects.
Most commonly, you’ll see SLA printing used for projects such as –
- Engineering prototypes
- Dental applications
- Rapid prototyping
- Short-run productions
Fused Deposition Modeling (FDM)
Fused deposition modelling (FDM) is also commonly referred to as fused filament fabrication (FFF) and is the most widely-used kind of 3D printing at the consumer level. This is because FDM printers that extrude thermoplastic filaments through a heated nozzle are fantastic for the low-cost prototyping of simple parts and models. These can then be improved upon using finishing processes like chemical and mechanical polishing.
FDM printers require filament types like ABS and PLA, and are best used for applications that include –
- Simple prototyping
- Hobbyist parts
- Proof-of-concept models
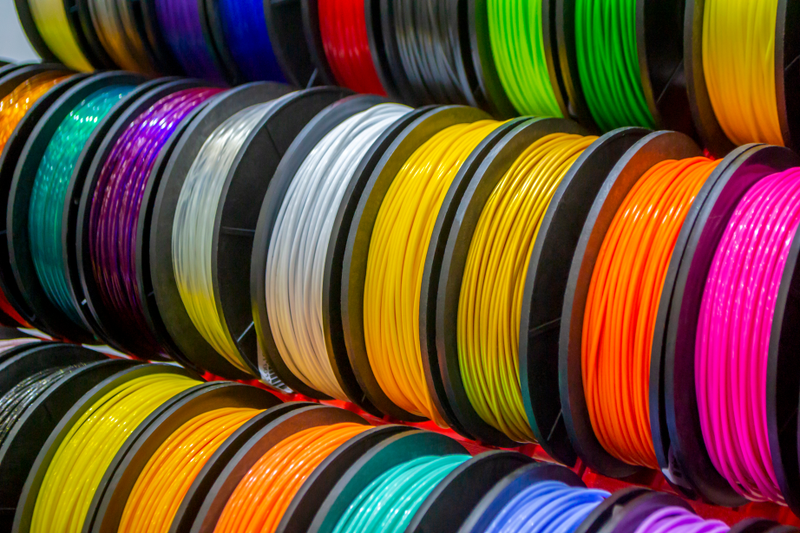
3D Printing Materials
The most common 3D printers typically require either resin or filament printing materials, the best of which will depend on things like build size and the level of detail required as follows –
Resin
Resin printers that use printing technologies like SLA or digital light processing (DLP), cure photopolymer liquid resins to create hardened plastics. This has the benefit of creating high-resolution parts with intricate details and smooth finishes. Resin printers can also typically print an entire layer of your model in one go, making for a pretty fast build. However, it’s also worth noting that resin printers are typically suited to smaller build sizes, and do limit you to a single resin during the building process. Resin models also typically require extensive finishing, including cleaning, washing, and curing. Common uses for resin printing include medical apparatus and props or models.
Filament
Filament printers use processes like FDM, which melts continuous filaments or thermoplastic materials (such as PLA and ABS) through a heated extruder to create layered 3D models. It’s possible to use either single or dual filament heads to achieve things like colour and material variations if you want them. Dual filament heads also enable the printing of two models at once, making resin generally preferable for things like customisation, and build volume. However, filament printing, especially for large or intricate builds, can be slower than other options. Layer lines may be visible on filament models which are also susceptible to warping. Filament is most often used for prototyping.
3D Printing Support Materials
Finishing a 3D print is a critical step that can significantly enhance the appearance and functionality of the object. Once the printing and support removal processes are complete, additional materials can be used for post-processing. These materials include sandpapers for smoothing surfaces, paints for adding color and detail, or sealants and varnishes to provide a protective coating. For objects requiring added strength or flexibility, epoxy resins can be applied. Additionally, metal plating can be used to give plastic prints a metallic finish, increasing their aesthetic appeal and structural integrity. Through the application of these extra materials, creators can achieve professional-level finishes, turning their 3D printed objects into masterpieces.
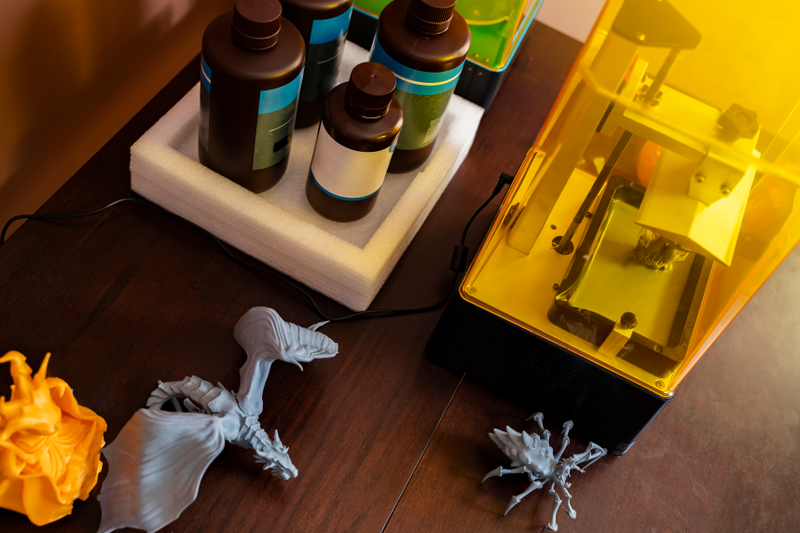
Benefits of 3D Printing
3D printing can be beneficial no matter your technical level. Choosing the right printing technology and materials for your projects and preferences can unlock a whole load of benefits that include –
- Design freedom: Traditional manufacturing takes design out of your hands, and brings additional limitations along with it. By comparison, self-led 3D printing design is completely customisable to your tastes, and makes previously unreachable goals, like internal integrations, easy to achieve.
- Speed of creation: 3D printing software makes it easy to create even detailed model designs, which your 3D printer can then create in as little as a few hours for smaller builds. This is compared with potentially weeks if you outsourced manufacturing elsewhere.
- Cutting costs: Even after purchasing your own 3D printer, affordable options on the market make this a cost-effective choice, especially when you consider the ability to cut out costs like labour and warehousing. 3D printing materials also tend to be affordable, especially if you slice your designs to ensure you’re only using what you need.
What Can Be Printed by 3D Printers?
It’s now possible to print almost anything using the right 3D printer and software. And that’s true no matter your technical skill. Undeniably, large builds with intricate parts require more detailed software, but even someone with a basic understanding can print small-scale models like tools or figures. The possibilities to create objects are endless and can help you create things such as a digital model to printed parts.
Some of the most impressive designs to come from 3D printing so far include –
- Robotic hands
- Human organs and tissue
- Dentures
Popular printing projects for beginners include bike accessories, keys, and beyond, all of which you can create with surprising ease once you’ve got the right equipment behind you. You simply need to do your research, invest in the right printers and software, and you’ll be ready to get started.
Discover 3D Printers at Jaycar
Embark on your journey into the limitless possibilities of 3D printing with Jaycar. Our carefully curated selection of 3D printers and supplies caters to enthusiasts and professionals alike, ensuring you find the perfect match for your creative or industrial needs. With Jaycar, you gain access to top-notch customer support, expert advice, and a community passionate about bringing ideas to life. Whether you're taking your first step into the world of 3D printing or looking to elevate your craft, Jaycar is your trusted partner. Discover the future of creation today by shopping at Jaycar, where we prioritise reliability, affordability, and the very best in 3D printing technology. Don't just dream about the future—print it, with Jaycar.